VIBRATION MACHINERY
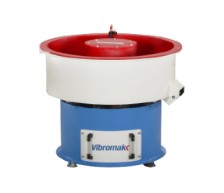
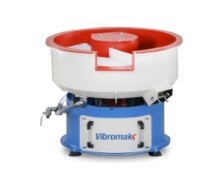
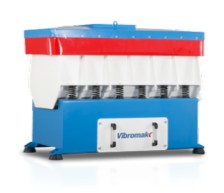
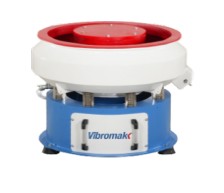
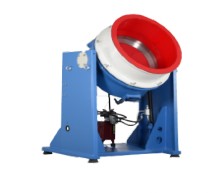
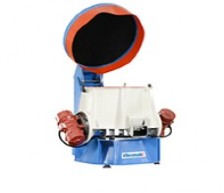
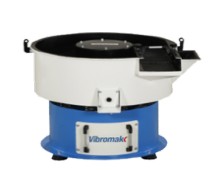
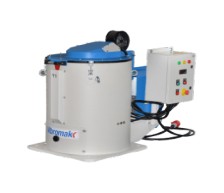
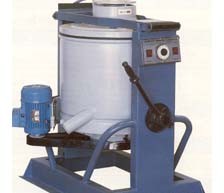
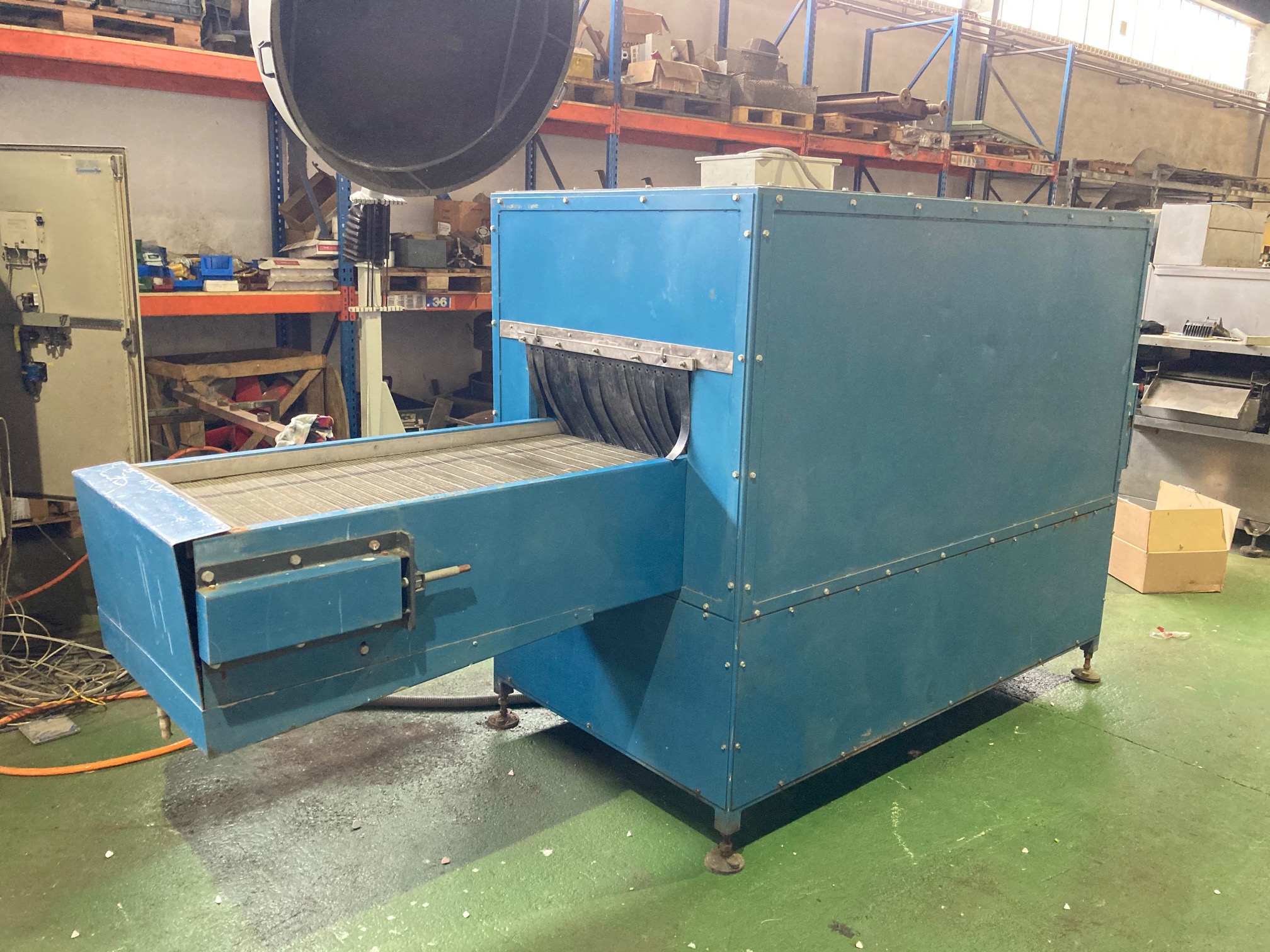
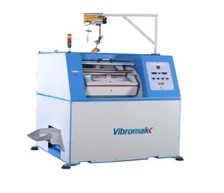
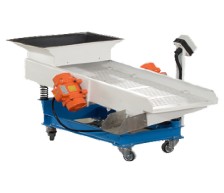
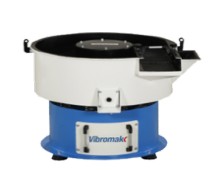
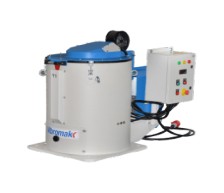
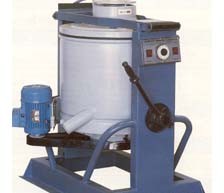
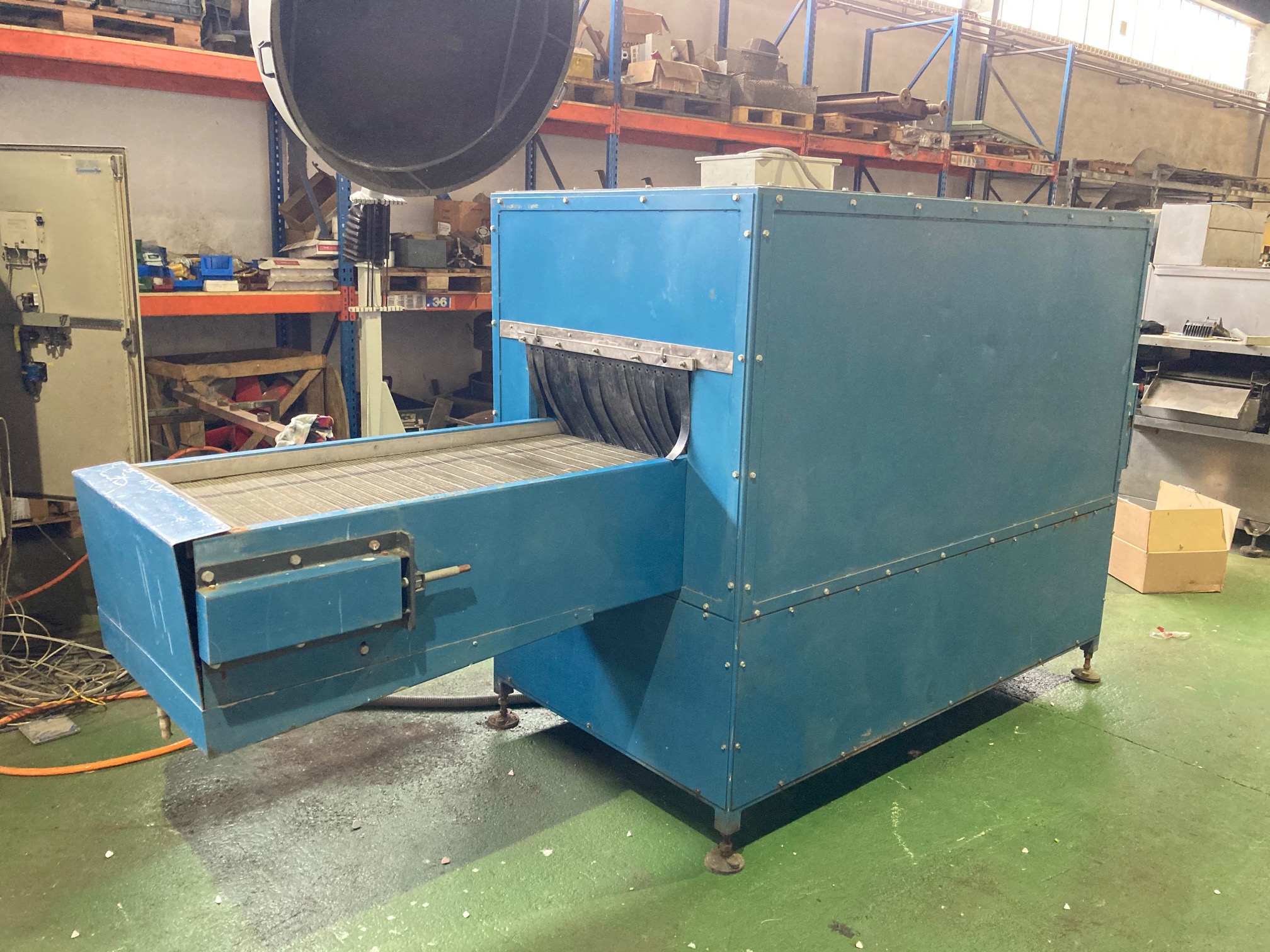
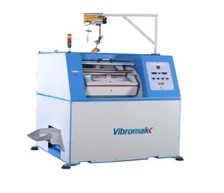
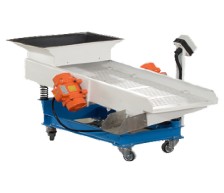
Vibro without discharge straight bowl
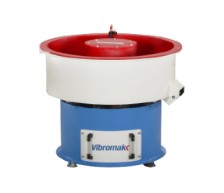
The simplest of our vibration machines. It consists of an eccentric motor and a working tank in polyurethane, without automatic unloading system. It has a higher useful capacity than its counterparts with unloading, but with the impediment that the pieces must be removed by hand or by means of a magnetic separator, (which is sometimes an advantage...). Capacities from 6 to 2,500 liters.
Documentation
Download InformationVibro with automatic discharge
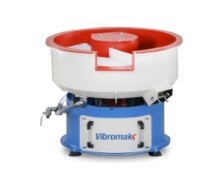
It is our reference machine in surface finishing by vibration. Excellent quality-price ratio of all our machines. The parts are automatically discharged through the discharge chute and abrasive-part separation sieve, with pneumatic drive of the discharge wedge. With capacities from 75 liters to 1,500 liters. Ask us what your problem is; we surely have the solution.
Documentation
Download InformationLinear Vibro
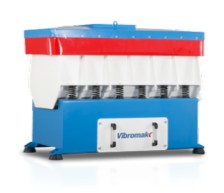
When, due to the dimensions of the part, the rotary vibrator is not enough, the rectangular vibrator has to be used. It is a very convenient machine for large and/or long and sensitive parts, being able to be treated even in independent compartments, to avoid the collision between them (this is the way our customers are working in aeronautics at the moment). We have a great variety of machine sizes and capacities. There are systems with discharge and without discharge.
Documentation
Download InformationVibro without discharge round tank
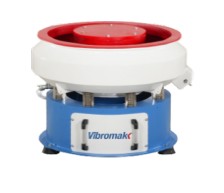
Vibro without unloading, with a rounded work bowl, so that the pieces rotate inside the machine in a more energetic and effective way. By incorporating variable speed drive, we can work with sensitive and delicate parts. Magnificent surface finishes with respect for the workpiece.
Documentation
Download InformationCentrifuges for turbo finishing
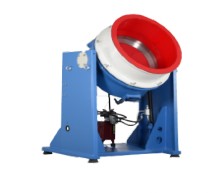
The Turbo centrifugal machines are characterized by high working speeds for all types of treatments such as deburring, pickling, radiusing, polishing,...). Compared to traditional vibration, the process times are significantly reduced, at a speed ratio of 6 to 1. We have machines with capacities from 3 to 150 liters (useful), for treatment of jewelry pieces or for industrial mass treatments. We can automate the whole process or supply only the working machine.
Documentation
Download InformationVibro for wheel polishing
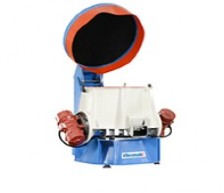
Vibration machine for deburring, polishing and buffing of rims up to 24 inches. This special design for wheel finishing is up to 30% faster compared to conventional polishing machines. It is applicable to both cast and forged aluminum wheels, restoration of classic car components and different types of engine parts.
Sawdust Vibro Dryer
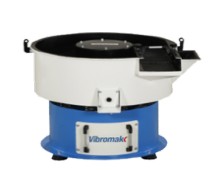
After vibration finishing, the treated parts must be dried as soon as possible. In this way we will avoid undesirable oxidation or risks of the pieces “taking” (as can happen with aluminum or brass). In these machines we use corn sawdust, of different sizes, depending on the pieces to be treated, and we can either heat the vat and heat the sawdust; or directly heat the sawdust using an electric resistance. With capacities from 80 to 1,200 useful liters. The unloading of pieces is done automatically, leaving the sawdust inside the tank to wait for the next batch of pieces.
Documentation
Download InformationCentrifugal dryer with extractable basket
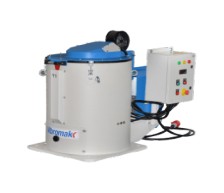
Today's quality requirements demand dry, shiny and spotless parts. With the centrifugal dryers, we remove tempering oils, machining oils, cooling and lubricating liquids, as well as water and humidity residues. The machines can be equipped or not with heating, speed variator, work timer, etc., depending on the requirements of the part. The baskets are always made of stainless steel, so as not to contaminate the parts we treat with oxides. In this model, the working basket is extracted either manually or by popilasto.
Documentation
Download InformationCentrifugal tumble dryer with tilting basket
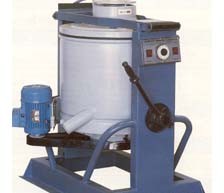
Today's quality requirements demand dry, shiny and spotless parts. With the centrifugal dryers, we remove tempering oils, machining oils, cooling and lubricating liquids, as well as water and humidity residues. The machines can be equipped or not with heating, speed variator, work timer, etc., depending on the requirements of the part. The baskets are always made of stainless steel, so as not to contaminate the parts we treat with oxides. In this model, the work basket is tipped either manually or automatically.
Documentation
Download InformationHot air tunnel dryer
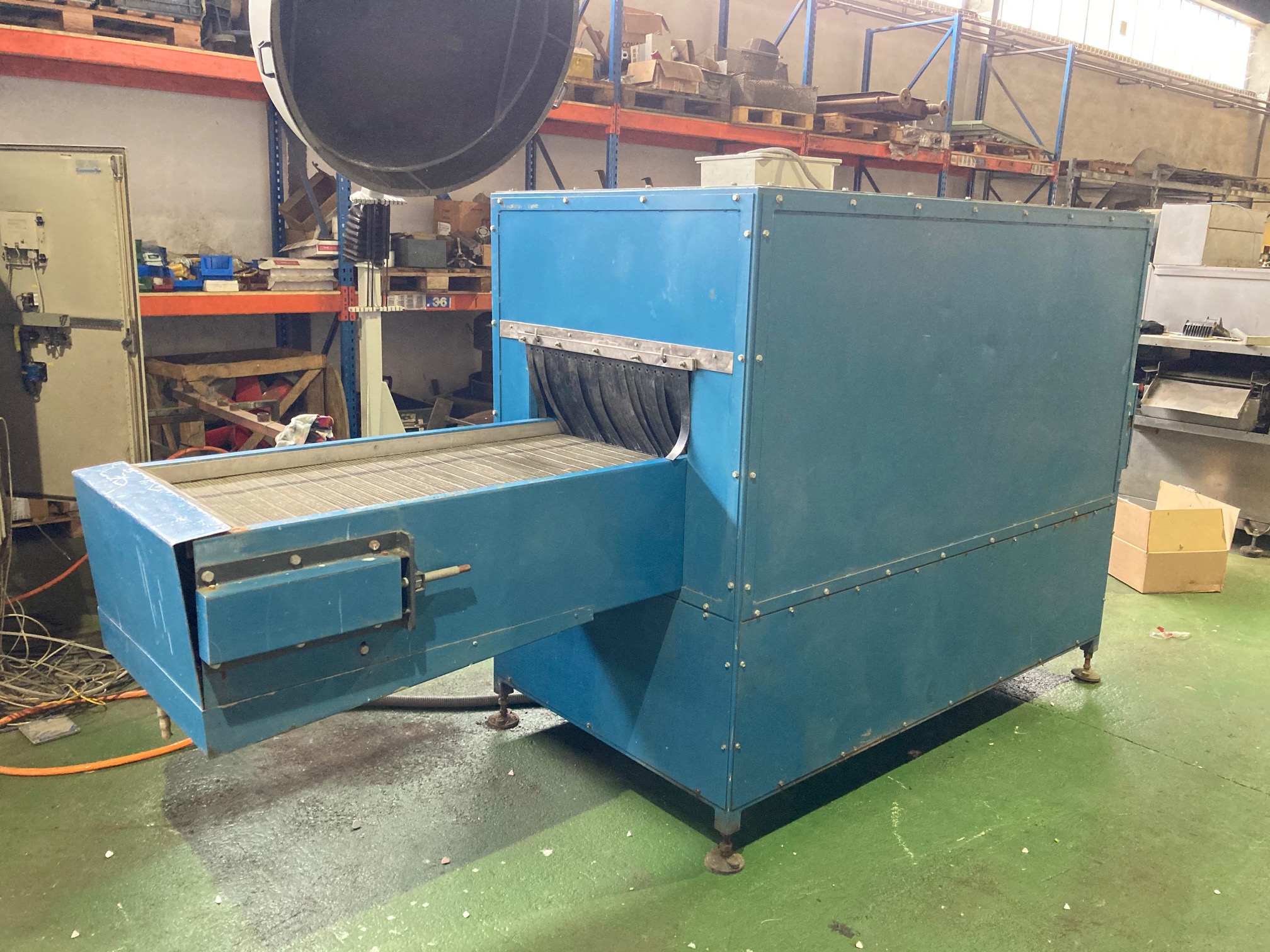
For parts that cannot rub against each other during the drying process or for parts with holes or cavities where sawdust could be lodged, we use belt dryers. Drying is carried out by means of a forced stream of hot air inside the tunnel. The belt is 500 mm wide and lengths between 1,000 and 3,000 mm, depending on the drying needs of the pieces being worked (on request we can manufacture belts 600-700-800 mm wide).
Air or sawdust drum dryer
Rotary drum dryers are used for rotating parts or parts that can be hit against each other. The parts are loaded continuously or in batches into the drum. Drying takes place either by a jet of hot air or by mixing with a drying product (sawdust, corn stover, etc.) During the rotation of the drum, the parts are enveloped in a drying product that removes the moisture from them or they receive a jet of hot air. The heating system located in the lower part of the drum evaporates the water and prolongs the absorbing power of the drying product. The profiles welded inside the drum guarantee the turning of the pieces (worm screw). At the end of the drum, the mixture of parts and product passes through a sieve where separation takes place. The pieces come out of the machine and the product remains inside.
Rotating drum for vibro-bubbling
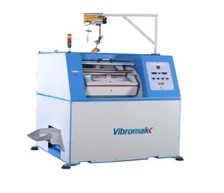
Older deburring system by drum rotation, but still in use for e.g. deburring and polishing treatment of buttons or small parts, resins, etc.
External sieve for abrasive-workpiece separation
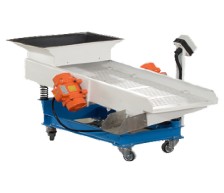
Systems external to the machines, to perform the automatic work of separating abrasive and parts, when emptying a machine. It is also used to perform separation screening of abrasives of different sizes, (e.g. selection of out-of-size abrasives in an operational mix).
VIBRATION PRODUCTS
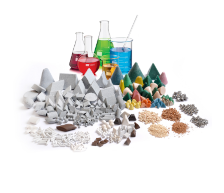
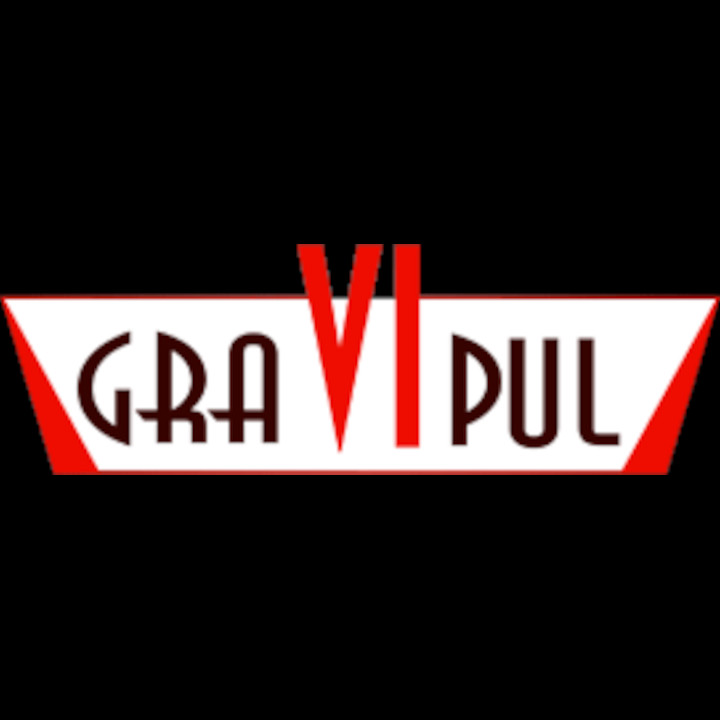
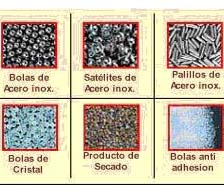
Ceramic-polyester-porcelain-ceramic consumables-chemical compounds
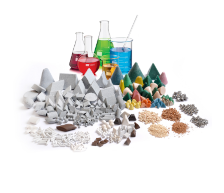
Abrasives, alkaline and acid compounds, grinding and polishing pastes. Wide variety of shapes, sizes and cutting grades, from extra-hard cut to soft or no cut. Ceramic abrasives: recommended for ferrous parts, stainless steel, etc.
Polyester abrasives: recommended for non-ferrous parts, such as aluminum, brass, copper, magnesium, etc.
Porcelain abrasives: recommended for polishing any material.
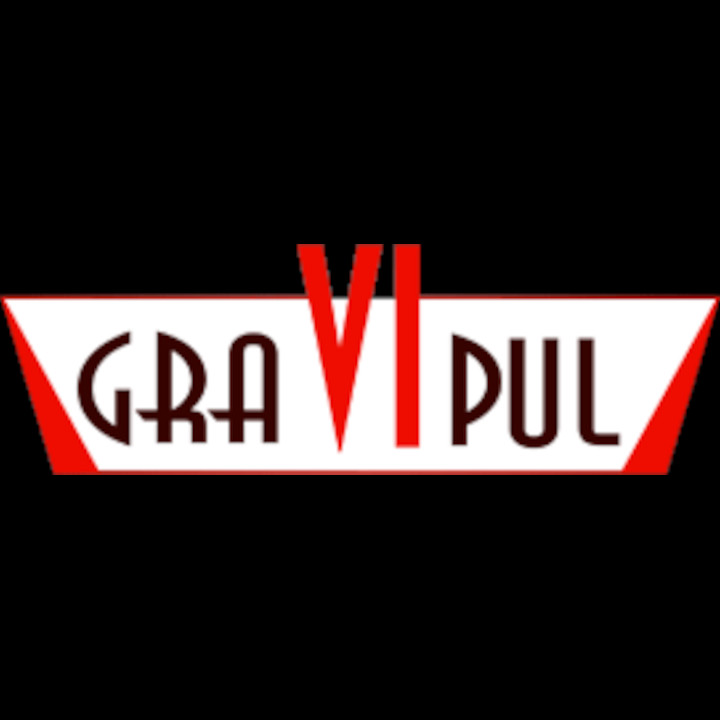
With this application, finishes down to Ra < 0.02 microns are achieved. Increased resistance to material fatigue due to bending and contact; reduction of noise and vibration of the parts; reduction of friction and wear; reduction of working temperatures; increase of power in competition engines; reduction of maintenance costs by extending the replacement time of parts; increase in the duration of gears, bearings, transmissions, etc. Treatment highly recommended for parts working in extreme environmental conditions, either for being outdoors (aeronautics) or inside high value added engines.
Stainless steel, sawdust, glass products
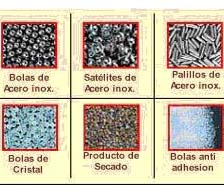
For parts polishing treatments, we use high quality stainless steel products, such as balls, sticks or satellites, in different sizes, for drying parts after vibration treatments, we use maizorb sawdust, with different thicknesses, in order to be able to cover the whole range of parts and geometries. Likewise, in vibration processes, we use our product RAT, to avoid the adhesion of flat parts during abrasive treatments, and grinding and/or polishing pastes. Request our catalog by e-mail